在“双碳” 目标指引下,我国能源革命势在必行。氢能作为众多一次能源转化、传输与融合交互的纽带,是实现碳达峰、碳中和的关键。目前,氢能应用主要在交通领域,加氢站作为产业链下游环节,是保障氢能燃料电池车产业发展,实现终端零碳排放的关键。PEM制氢设备采用现场谷电电解水制氢与外购氢互补的形式作为氢源,不仅能丰富上游气源,保障加氢站的稳定运营,通过“削峰填谷”降低氢源成本,还有利于减少氢气长管拖车运氢对城市安全带来的潜在风险,被视为最适合城市加氢站建设发展的路径之一。两路气源的制氢加氢系统,如何实现高效的深度融 合, 提 高 整 体 效 率, 是 需 要 解 决 的 首 要 问题。目前,加氢站主要以高压氢气进行加注,核心关键设备为氢气高压压缩机,尤其是45MPa氢气压缩机。同时,由于国内技术水平相对落后,进口 45MPa氢气压缩机占据加氢站主要市场,压缩机的成本占加氢站总投资的约50%。同时,由于整站压力、温度最高的情况均出现在 45MPa 氢气压缩机条件下,后期运营维修也多。因此,文中从降低 45MPa氢气压缩机负荷,提高整站效率与经济效益等角度出发,进行现场制氢与外购氢结合加氢站系统工艺优化研究。 针对常规的现场制氢与外购氢结合加氢站系统进行优化,提出一种优化方案。同时,为了对比常规工艺与优化工艺在能耗、经济性方面的差异,以某现场制氢与外购氢结合加氢站系统为例,进行计算模拟对比分析。 水电解制氢设备
该加氢站加氢量为 500kg/d,制氢装置的规模为300m3/h,谷电时长为8h。经计算,加氢站现场电解水制氢能力约为 214kg/d,其余 286kg 氢气采用外购氢补充。外购氢通过长管拖车进行输送,长管拖车充满时压力为 20MPa。制氢装置出口压力为3MPa,温度为 30℃。终端加氢压力为 35MPa。 如图 1 所示,在谷电时期,以现场制氢装置为主,进行现场制氢。制得的氢气压力约为3MPa,经过滤器通入20MPa氢气压缩机。加压后通入20MPa储罐。储罐出来的氢气通入45MPa氢气压缩机,加压至 45MPa,再通过水冷系统冷却至 30-45℃。而后通入 45MPa储罐。当下游有用氢需求时,45MPa储罐内的氢气依次经过顺序控制柜、加氢机加注至车载储氢瓶中。在非谷电时期,制氢装置关闭,以外购氢作为氢源进行运营。氢气长管拖车内的高压氢气经过卸气柱接入45MPa氢气压缩机,进行加压储存至45MPa储罐中,以供后端使用。在实际运营中,受现有45MPa氢气压缩机性能的限制,氢气长管拖车内的氢气压力低于7MPa左右时,压缩机出口氢气温度过高,卸车速率较慢,多数加氢站便停止卸车。如图2所示,文中提出了一种现场制氢与外购氢系统结合工艺优化方案,基于现有设备,在卸气柱后设置一段支路。当长管拖车内压力较低时,关闭主路阀门,打开支路阀门,卸气柱出口氢气通过压力调节阀,调节至1-3MPa后,先通入20MPa氢气压缩机,加压冷却后,通入20MPa储罐,再通过45MPa氢气压缩机加压,供后端使用。
以氢气终止卸车压力为1MPa为例,计算不同卸气柱出口氢气压力下,原工艺与优化工艺将氢气加压至45MPa所需的能耗与对应的压缩机出口氢由图3可知,对于仅有主路的原工艺,当卸气柱氢气出口压力高于 7MPa时,系统能耗低于75kW,45MPa氢气压缩机的出口温度低于300℃,能耗与温度增加的速度同时较为缓慢;当卸气柱氢气出口压力低于7MPa左右时,由于压缩比较大,45MPa氢气压缩机能耗与出口温度分别骤增至90kW与300℃以上。不仅造成能耗的增加,也对设备材料提出了更高的要求,提高了设备的投资。高纯氢气发生器
通过在原工艺基础上增加支路,以7MPa作为切换压力。当压力低于7MPa时,将卸气柱出口氢气通过支路调压后再依次通过20MPa氢气压缩机与45MPa氢气压缩机加压至45MPa,系统能耗可稳定在75kW左右,同时控制45MPa氢气压缩机的温度低于150℃;当压力高于7MPa时,依然采用原工艺主路,将卸气柱氢气直接通入至45MPa氢气压缩机。优化工艺通过主路、支路配合,不仅能降低压缩机负荷,确保压缩机出口温度不超过250℃,稳3定45MPa氢气压缩机工况,延长压缩机使用寿命。
在实际操作中,为了避免当卸气柱氢气压力低于7MPa时,导致的45MPa氢气压缩机出口温度过高的现象,仅卸车至7MPa左右。本文提出的优化工艺,除了在提高系统性能、保护45MPa氢气压缩机方面效果显著外,还可降低氢气终止卸车压力,提高氢气长管拖车的氢气有效卸车量。
以载氢量为380kg,储氢压力为20MPa的氢气长管拖车为例,分别计算不同氢气终止卸车压力条件下的卸氢量与氢气成本,结果如表 1 所示。由表 1 可知,以氢气终止卸车压力为2MPa为例,优化工艺能够提高长管拖车38.46%的有效卸氢量,同时降低储运成本,使到站氢气成本从 42.15元/kg降低至 38.77元/kg,降低了8.02% 。虽然,卸气柱出口氢气压力低于7MPa时,受 20MPa氢气压缩机入口压力范围的要求,需要将氢气调压至2MPa,再依次加压导致系统加压氢气能耗略有提高,平均加氢能耗从 1.48元/kg增加至1.62元/kg,但由于增幅较小,最终氢气出售成本从 43.11元/kgg降低至 39.82元/kg,降低了 7.63%。当氢气终止卸车压力由3MPa降至1MPa时,对有效卸氢量和氢气出售成本有一定影响,有效卸氢量由323kg增加至 361kg, 与 旧 工 艺 相 比 增 幅 为 30.77% —46.15%;平均加氢能耗略有增加,从1.56kW/kg 增加至1.69kW/kg,但由于增加了有效卸氢量,氢气出售成本依然呈降低趋势,即从 40.30 元/kg降低至 39.41元/kg,与旧工艺相比,降幅为6.52% —8.58%。由此可知,当购氢成本为30元/kg时,通过此优化工艺将氢气尽可能多地卸车,能有效降低氢气出售成本。
计算不同氢气终止卸车压力下,购氢成本从5元/kg增加至40元/kg时的氢气出售成本,结果如图 4 所示。
由图4可知,购氢成本会对氢气出售成本造成影响。通过优化工艺,降低氢气终止卸车压力,能有效降低氢气出售成本。当购氢成本从40元/kg降低至5元/kg时,优化工艺的氢气出售成本均低于原工艺,但降低程度呈减缓趋势。(1)优化工艺可避免低压氢气直接通入45MPa压缩机,导致压缩机压缩比高,确保压缩机出口温度不超过250℃,避免排气温度过高造成机头材料受损的现象,稳定45MPa氢气压缩机工况,进而提高加氢站核心设备45MPa压缩机的寿命,保证加氢站稳定高效运行。(2)通过设置卸气柱后端支路,可将氢气长管拖车内的氢气从常规的 7MPa降低至3-1MPa。可提高拖车内氢气利用率30.77%—46.15%,进而降低到站氢气成本6.79%—9.11%。虽然通过支路会增加氢气加压能耗,但由于增幅较小,最终优化工艺仍能降低氢气出售成本6.52%—8.58%。(3)在购氢成本在5-40元/kg时,优化工艺在降低氢气出售成本方面具有优势。同时,随着购氢成本的降低,优化工艺在降低氢气出售成本方面的优势呈下降趋势。
总之,本文通过在常规现场制氢与外购氢结合系统的基础上,通过设置支路,能对保护 45 MPa 氢气压缩机,提高长管拖车有效卸氢量,降低氢气出售成本方面具有显著的作用,可为实际生产运营提供参考。
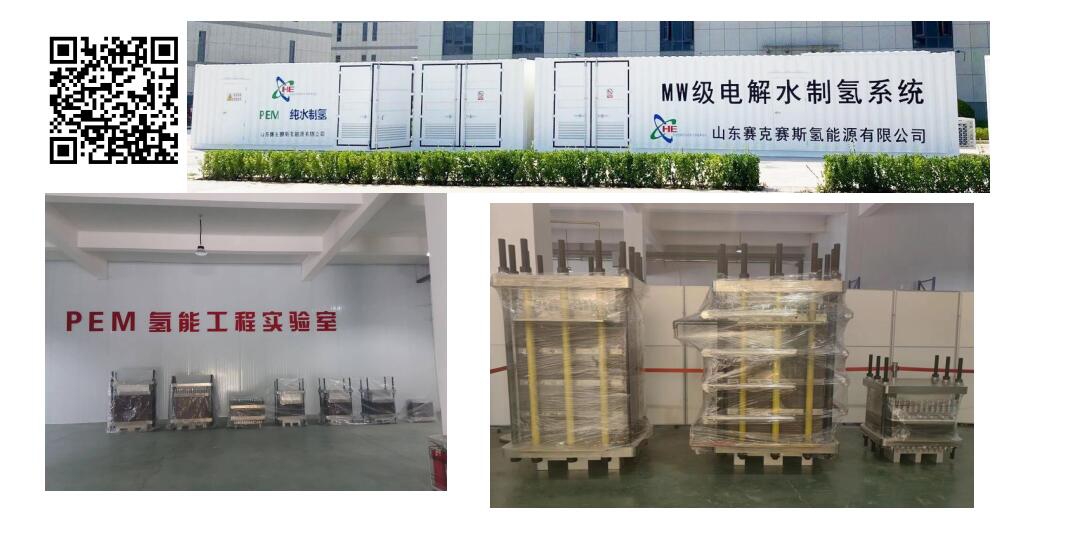