PEM电解水技术,将水分子电离为OH-和H+、通过质子交换膜(PEM膜)传输H+,生成氢气、氧气和可循环使用的水,不需要添加液体电解质,可以避免ALK使用强碱性液体电解质,实现洁净排放。由于PEM槽的阳极处于强酸性和高电压环境、阴极处处于强碱性环境,阳极的非贵金属容易被腐蚀、并容易与PEM膜中的磺酸根离子结合进而降低H+传导能力,因此更依赖难加工的钛合金和铂、钯、钌、铱等贵金属,导致成本过高。
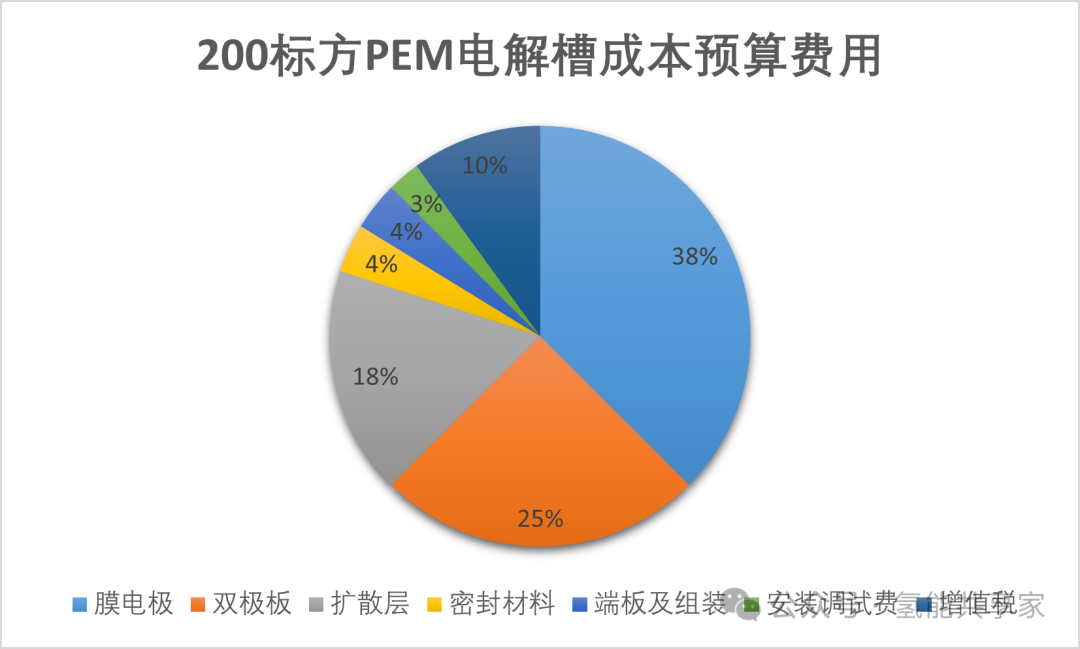
200标方的PEM电解槽成本中,膜电极占38%,双极板占25%,扩散层占18%,这三部分占比达到80%以上了,其中膜电极占据PEM电解槽的主要成本,占比最大,膜电极的主要组成是质子交换膜、析氧催化电极和析氢催化电极。PEM电解槽降本能降多少,技术有怎样的进步,就看这三分部分的技术水平发展。
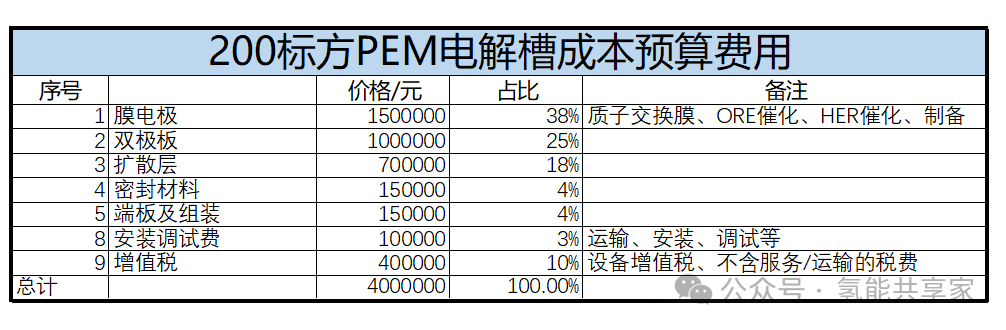
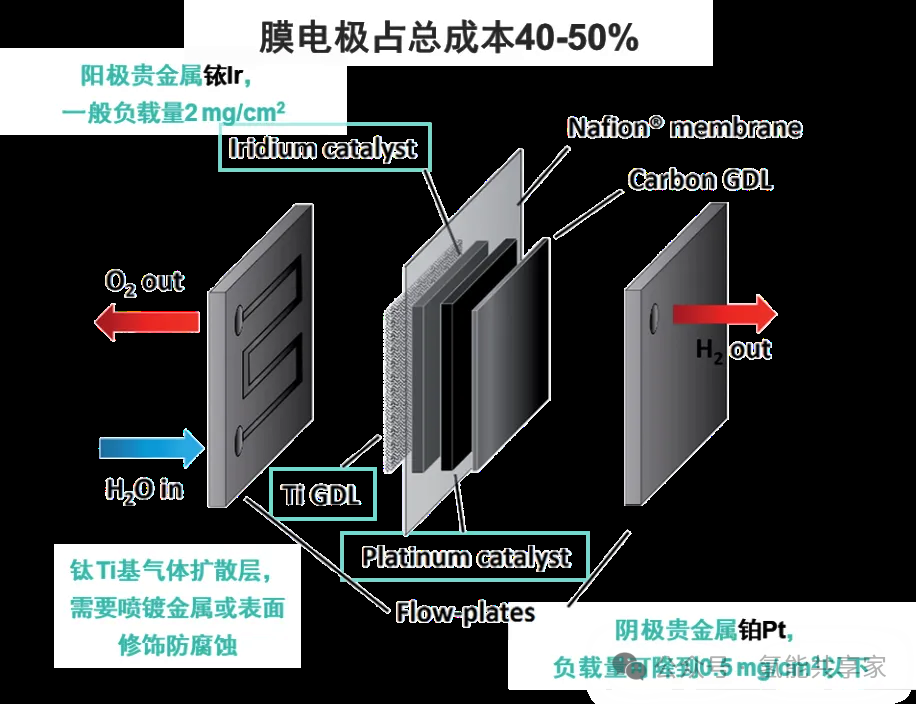
目前PEM电解槽主要有四类玩家:
一、PEM电解水的独立企业,只做这一种技术路线,在行业内时间也较长,有一定的名气,或者是一些科研院所孵化而来,或者是从其他厂家裂变而来;
二、燃料电池企业转型,燃料电池本身也类似PEM电解槽,从原材料到结构器件相似度比较高;
三、ALK槽企业或其他领域装备厂家业务扩张,作为技术储备而发展PEM槽技术,押宝各种技术路线;
四、氢气终端用户或气体运营商向上游拓展业务,自主发展和并购并行。国产装备全面崛起后将对供应链带来积极影响。
PEM电解槽部分材料器件还依赖进口,但随着制氢行业的发展,制氢成本的压力,国产化进程加速,成本也在快速下降。随着PEM电解槽向大标方、高电密、低成本等方向发展,对核心部件PEM膜、催化剂、气体扩散层、双极板等提出新的要求,国产供应链迎来弯道超车的机会。
1)以前PEM膜依赖进口,国内外技术差距较大。但现在国产头部企业市场占有率在逐步上升。
2)PEM槽的贵金属基电催化剂主要使用的Pt和Ir等贵金属,在国内的储量较少,需从南美、南非、俄罗斯等地区进口。
3)PEM槽的气体扩散层的进口依赖度较高。目前国内可以生产钛基扩散层的企业较少,仅在民用PEM槽领域取得应用突破,但工业级PEM槽的扩散层产品仍以进口品牌为主。
4)PEM槽的双极板基本都为定制化产品,难点在于提升加工精度和降低成本。国内目前能设计并制造PEM槽双极板的企业相对较少。
5)PEM膜电极常用涂覆工艺,但预计未来会有电化学沉积等更多制备方法来改善质子传导率、贵金属利用率和电化学性能。
6)膜电极的降本主要在原材料的改性和国产化降本、自研独特的涂覆工艺两方面,因此PEM膜、电极、催化剂公司纷纷储备膜电极技术,电解槽公司也积极向上游渗透、以降低成本,独立第三方膜电极厂家的生存空间被挤压、被迫往上下游发展方向。
1、PEM电解槽的优势:
1)PEM槽的隔膜比较薄,阳极/阴极/隔膜采用零间距结构,内阻较低;
2)PEM以纯水为反应物、清洁排放,且质子交换膜隔离了氧气、因此氢气纯度较高,后端仅需脱离水蒸气、无需增加其他气体提纯/反应装置;
3)压力调控范围大,输出压力可高达数兆帕,提供高压氢气,减少压缩空气的功耗;
4)可适应快速变化的能源输入、尤其波动性的风光绿电,具备宽负荷工作能力;
5)可在较高电流密度(>20000A/m2)工作,利于降低成本。
2、PEM电解槽的缺点:
1)当价格过高,按照相同功率或产氢量的采购成本达到ALK槽的近3倍,源于行业规模小、采用贵金属、单体功率和产氢量规格小等原因;
2)PEM槽若适应绿电的波动性,则全天平均功率仅约30~50%、产能利用率较低,若采用储能电池则投资额度会明显增加,若引入网电则没有利用好PEM技术优势;
3)全氟磺酸酯膜的国产化进度慢于ALK的PPS膜国产化进度;
4)减贵金属研究尚不充分。
海外市场青睐PEM路线、PEM项目占比高,主要有产业积累、政策导向和应用场景等几大原因。
1)海外PEM电解槽产业的历史积累久、全产业链各环节均培育出优势企业。
2)现阶段PEM制氢技术更能符合欧盟的碳中和政策。欧盟对于绿氢的可再生电力来源要求苛刻:在制氢工艺环节必须使用绿电,而现有技术条件下,PEM电解槽更能适应可再生能源等波动电源。
3)欧美的应用场景较单一,设备规格偏小,技术相对成熟且成本不高。考虑到单个项目可能有多台设备组成,因此这些项目普遍规模应该单台设备小于1MW、制氢能力不超过200Nm³/h,相对技术成熟,总投资额也不高、在这些大型企业承受范围内。但若追求极致的成本控制,则采用大规格设备势在必行。
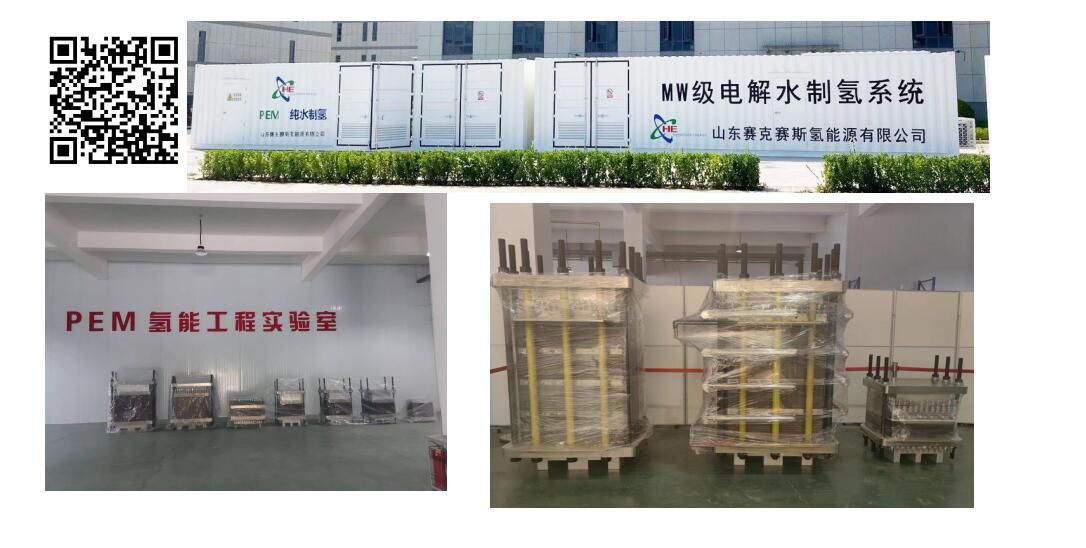